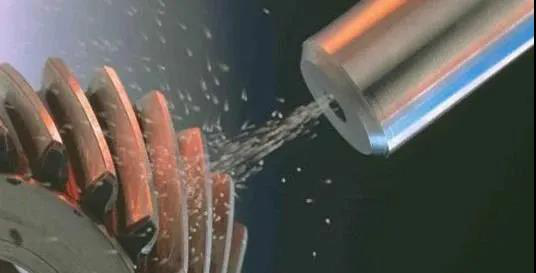
现代表面处理工艺日新月异,但作为传统的表面前处理工艺----抛丸、喷丸和喷砂却经久不衰,市场上使用面还是很广很宽,但三者的区别和应用场合往往大家比较迷惑,今天把它讲讲清楚给大家带来帮助。
喷丸处理(shot peening)是工厂广泛采用的一种表面强化工艺,即使用丸粒(直径1-2mm金属粒子)在压缩空气的推动下轰击工件表面并植入残余压应力,提升工件疲劳强度的冷加工工艺。广泛用于提高零件机械强度以及耐磨性、抗疲劳和耐腐蚀性等。
喷丸处理的优点是设备简单、成本低廉,不受工件形状和位置限制,操作方便,缺点是工作环境较差,单位产量低,效率比抛丸低。喷丸的种类有钢丸、铸铁丸、玻璃丸、陶瓷丸等。
与喷砂的区别
喷砂也是使用高压风或压缩空气作动力,将其高速的吹出去直径100目左右的砂粒或者1mm左右的砂丸冲击工件表面达到清理效果,但选择的介质不同,效果也不相同。喷砂处理后,工件表面污物被清除掉,表面积大幅增加,从而增加了工件与涂/镀层的结合强度。
经过喷砂处理的工件表面为金属本色,但是由于表面为毛糙面,光线被折射掉,故没有金属光泽,为发暗表面。
喷丸处理后,工件表面污物被清除掉,工件表面被微量进而不容易被破坏。表面积有所增加。由于加工过程中,工件表面没有被破坏,加工时产生的多余能量就会引起工件基体的表面强化。
经过喷丸处理的工件表面也为金属本色,但是由于表面为球状面,光线部分被折射掉,故工件加工为亚光效果。
与抛丸的区别
喷丸使用高压风或压缩空气作动力,而抛丸一般为高速旋转的飞轮将直径2-5mm钢丸高速抛射出去。抛丸效率高,但会有死角,而喷丸比较灵活,但动力消耗大。
两种工艺虽喷射动力和方式不同,但都是高速冲击工件为目的,其效果也基本相同,相比而言,喷丸比较精细,容易控制精度,但效率不及抛丸之高,适形状复杂的小型工件,抛丸比较经济实用,容易控制效率和成本,可以控制丸料的粒度来控制喷射效果,但会有死角,适合于形面单一的工件批量加工。
两种工艺的选用主要取决工件的形状和加工效率。
总结如下:
| 动力源 | 材料 | 尺寸 | 处理目的 |
喷丸 | 空气 | 金属粒子 | 1-2mm | 精密强化材料表面 |
喷砂 | 空气 | 非金属砂粒 | 100目、1mm | 除锈、增加表面积 |
抛丸 | 旋转飞轮 | 金属粒子 | 2-5mm | 高效强化材料表面 |
齿轮等工件适合喷丸处理
【本文为我司原创文章,如需转载,请与我司联系。】